REPAIRS, REHABILITATION AND RETRO-FITTING |
|
REPAIRS, REHABILITATION, AND RETROFITTING BY FERROCEMENT |
• |
Most effective as it is structural treatment |
• |
Vibration and wiremesh Reinforced |
• |
Layers make the mortar dense and crack resistant |
• |
Most durable treatment even after one and a half decades |
• |
Fire resistant upto 750oC for 48 hours |
• |
Can be made to resist high temperature |
• |
Existing room area can be extended by a meter or so |
• |
Jacketing of column and beams 40-50 mm thk. |
• |
Prevention of buckling of columns. |
• |
Crack formation along reinforcement even after repairs by other systems shall not take place |
•
|
Research on repairs with Ferrocement Technology has proved that RCC members improve in strength by 125% to 300% as compared to original undamaged condition. |
|
Ferrocement Cantilever |
can be planned to be Longer than R.C.C. Cantilever because of less Self-weight and high strength. These Canti- levers can take earthquakes and cyclones more efficiently than R.C.C. |
|
|
|
Ferrocement Balcony |
• |
much lighter than R.C.C. |
• |
Best against earthquake and cyclones |
• |
Best replacement to crashed R.C.C. balcony |
• |
new balcony can be attached to entire building |
• |
No disturbance to the occupants |
|
|
Weather shed Chhajja attachment with Ferrocement plates |
• |
Attachment by innovative anchoring system |
• |
joint with building totally waterproof |
• |
Integrates with building |
• |
Brackets generally provided for conventional are eliminated |
|
|
REPAIRS, REHABILITATION AND
RETRO-FITTING |
Significance of Ferrocement repairs |
After, we in India, started manufacture of concrete in years 1930’s, the negative aspect of concrete started showing after sometime as below:- |
- Deterioration due to poor workmanship, particularly high water content and corrosion of reinforcement and R.C.C. Technology being new. |
- Leakages in concrete due to rain water as well as in water retaining structures |
This menace become conspicuous after construction works which became old about 20 to 30
years. We started realizing the importance of water cement ratio that only since about 40 years
before and we have become very much conscious and now most of our engineers try their best to
have Water cement ratio to the extent of its requirement. Even then, we did not stop production
of concrete with water content comparatively more. It had been accepted that concrete is
heterogeneous material and theory of reinforced concrete design is on the basis of cracked section below neutral axis. With this acceptance, scores of water proof additives and other admixtures contributing to the increase in strength, durability, workability and waterproof quality of concrete have come into market. Now it is a foregone conclusion that you cannot have best quality of concrete unless admixtures are used in its manufacture. Also many instruments for diagnosis for defective concrete such as porosity, lamination of cement matrix with course aggregate, corrosion of reinforcement, location of corroded reinforcement, strength of concrete etc. have come in the market in a very big way. Systematic method of inspection observations with measurements of the defects in concrete in a qualitative and also in quantitative manner have been developed and schemes / system of management of diagnosis analysis to maintain / to restore water proof quality and repairs to its original strength have been developed. |
All the above methods / system of water proofing, repairs and rehabilitation of structure costs lakhs of crores of Rupees to the nation. In order to save such expenditure, in-convenience, loss of time and energy CAN WE NOT PRODUCE A CONCRETE FREE OF SUCH DEFECTS? |
The quality of concrete can be improved to a large extent now. We are able to produce concrete
of strength M100 or even sometimes M 200 with least reason for corrosion of reinforcement.
Now a days corrosion of reinforcement is prevented by epoxy coating and galvanizing of
reinforcement. Because of theory of reinforced concrete with provision of design of cracked
section, the defects are bound to develop in due course of time which may be delayed. Prestressed concrete is the solon to a large extent with pretension structures. However
there is possible corrosion in post tension structures due to errors in proper grouting of cables. In any case structures now should be better than before. |
Concrete is heterogeneous material. It has features to loose bond with aggregate and steel reinforcement at early stages. It can be said it is not possible for concrete structure to last for hundred years. |
Now it is the time when we should think of concrete which should not crack at all and there should be no extra water more than required for reaction with cement. And concrete should
not crack at all when put under design loads. That means we must view or think about the theory of reinforced concrete that is a structural member is designed as cracked section cracking accepted below neutral axis. Or crack formation can be thought to be delayed. In other words crack width and minimum depths to stop entry of corroding forces upto reinforcement. Also the crack width should be so minute and depth should be so shallow that water be trapped in stopping it to travel below upto the bottom of the depth or reach reinforcement surface. The effect of atmospheric pollution or carbonation can be minimized/eliminated by use of certain admixtures in the concrete. |
|
Ferrocement Technology is the solution |
Under laboratory loads Ferrocement bends largely alongwith reinforcement without cracking.
Under further loads, several cracks do take place, width being very negligible to few microns.
Under very large loads only little wider cracks of low value less than 0.1mm take place. After this, structure will deform greatly but no collapse can take place. However on release of loads the cracks close. The deflection recovery has been found to be 97%. Sometimes it is said it has inbuilt property of prestress concrete to less extent In view of this significant feature of Ferrocement it is termed to have mechanism called ‘Crack arrest mechanism’ |
Corrosion of Reinforcement |
The corrosion of reinforcement in Ferrocement is most insignificant. The water cement ratio is
the least giving least extra water to react with wiremesh reinforcement. There may be corrosion of brown colouring with wiremesh reinforcements which is not strong enough to burst cement
matrix. In view of evenly spread wiremesh reinforcement, the corrosion is the most negligible
and can be said to be not at all causing any damage. We can say the minute corrosion is dormant in the case of Ferrocement. This is the feature of Ferrocement unless it is manufactured with inferior materials and inferior workmanship in slipshod manner. In view of this and cement
matrix being of superior quality, spalling / splitting will not take place. |
We have been practicing Ferrocement Technology since more than 25 years by now. In our
Ferrocement products, we maintain water cement ratio to be 0.35 to 0.4. We invariably vibrate our Ferrocement products either on machinery set up under controlled conditions or in- situ. In all our products to make it dense, we use admixtures to produce maximum strength and add many positive aspects to the materials. We use non- metallic fibers in the top of finished matrix. In view of such method of manufacture, we do not find any deterioration of our product and no problem so far as water proof quality of Ferrocement is concerned. In our Ferrocement products, there is no carbonation phenomena. We claim our method of manufacture is most meticulous with high quality and superior materials and workmanship. We are confident that our structures are bound to perform in a far superior manner. |
|
Historically Ferrocement has proved to be durable and without corrosion as below:- |
- A small Ferrocement boat constructed in 1887 was in operational condition till 1968 after
which it was shifted to lounge of the Vereniging Nederlands Cement industries’ office in
Amsterdam. |
|
- Several structures constructed by Mr. Pier Luigi Nervi during early 1940’s in number of
cities in Italy have been reported to be in good condition. |
- During 9th International Symposium, Prof. Khan A.M. in a joint paper alongwith Prof.
Rafeeqi S.F.A. and
- During 9th International Symposium, Prof. Khan A.M. in a joint paper alongwith Prof.
Rafeeqi S.F.A. and Prof. Lodi S.H. from Karachi, Pakistan presented a paper “Performance of Park Structure made by Ferrocement”. They carried out experiment to study condition of a water storage tanks from the point of view of durability and corrosion constructed by students of Engineering college in about 1993. He has concluded that the water tank structure made up of Ferrocement material has sustained the atmospheric condition satisfactorily. No significant corrosion effect of wiremesh was visible. |
|
In our experience with Ferrocement Technology at international level having attended all the Nine International Symposiums we have not come across any structure that has collapsed or is damaged due to corrosion. |
|
As a matter of fact, United Nations Industrial Development Organisation (UNIDO) have published a book in 1972 ‘Ferrocement boats’ and recommended the use of Ferrocement Technology at the earliest. |
|
Food and Agricultural Organisation (FAO) of UNO (United Nations Organisation) organized
international conference, Ferrocement fishing boats in the year 1972. It has recommended
adopting Ferrocement Technology for fishing vessels in view of Ferrocement being a sound
technology. |
|
Similarly, Royal Institute of Naval Architecture (RINA, UK) and National academy of
Sciences of USA have recommended in about 1972 use of Ferrocement technology as early and
as fast as possible. |
|
For the present international Ferrocement society, Bangkok, founded in 1991 and Committee
549 of USA and certain publications by RILEM, Paris, have been guiding by publishing
documents for the design and construction of Ferrocement structures. |
|
REPAIRS |
|
Ferrocement Repairs And Rehabilitation |
Visa-vis Polymers/Guniting Repairs And Rehabilitation |
Sr.
No. |
Ferrocement Repairs and Rehabilitation System |
Polymers/Guniting Repairs and Rehabilitation Treatment |
1 |
Ferrocement repairs and rehabilitation system can increase strength of columns, beams, and
slabs by 30% to 15% or even more. |
Polymer/guniting repairs and rehabilitation system cannot contribute to increase in strength of structures. |
2 |
Ferrocement repairs and rehabilitation system contributes to prevention of cracks formation. |
Polymer/guniting repairs and rehabilitation treatment can contribute little bit to prevention of cracks formation. |
3 |
Ferrocement repairs and rehabilitation system material does not allow penetration of water, atmospheric gases etc.
|
Polymer/guniting repairs and rehabilitation treatment material can prevent little bit entry of water and atmospheric gases in due course of time. |
4 |
Ferrocement repairs and rehabilitation treatment resist fire up to 750oC and higher for long period of 48 hours and more. |
Polymer treatment looses strength heavily at about 50-60oC and guniting at about 200oC. |
5 |
Ferrocement repairs and rehabilitation treatment is waterproof
|
Polymer/guniting repairs and rehabilitation treatment is not waterproof. |
6 |
Ferrocement chhajas can totally replace deteriorated crashed RCC chhajas with dead load reduction. Even where there is no RCC chhaja- new ferrocement chhaja can be attached to building. |
Polymer/ guniting system can not replace crashed/ collapse RCC chhaja. New RCC chhaja can not be attached to building. At the most new weather shed with A.C. sheet/ FRP/GI sheet can be attached but no assured waterproof at the junction. |
7 |
Jacketing of columns, beams, with ferrocement is about 30mm thick and adds strength. |
Jacketing of columns, beams, is 7.5cm thick, occupying large space; may/may not add strength. |
8 |
Ferrocement repairs and rehabilitation system is assured and guaranteed.
|
Polymer/ guniting is generally not assured and guaranteed treatment. |
9 |
Ferrocement repairs and rehabilitation can conveniently repair RCC sagging slab with dead load reduction. |
RCC sagging deteriorated slab repairs is cumbersome, time consuming and costly
|
10 |
Crashed RCC balcony can be totally replaced by ferrocement balcony with ferrocement chhajas, without disturbance to occupants inside. This balcony can have drop on sides with dead load reduction. |
Crashed RCC balcony repairs by RCC balcony is cumbersome costly and disturbance to occupants inside. Some times balcony provision is cancelled. |
11 |
Ferrocement Repairs and rehabilitation treatment is highly reinforced with small dia wire mesh two layers at least with unreinforced matrix size 6.00x6.00x1.5mm with low water cement ratio of around 0.4 |
Polymer treatment is without reinforcement. Guniting is reinforced with weld wire mesh generally 10g and even 75x75mm single layer only, thickness 40mm or so. Polymer treatment generate cracks along reinforcement in due course of time |
12 |
Ferrocement finish surface is smooth/sand faced |
Inevitable rough surface of guniting require sand face/smooth plaster. Thus extra expenditure. |
|
|
Repairs/ (Replacement) of (Crashed) RCC Chajja, Balconies with Ferrocement Technology |
- RCC chhajas is of a building show sign of deterioration after 15-20years or some times early. |
- Initially, there is cracking of plaster, peeling of cover of concrete and beginning of corrosion of steel reinforcements. |
- If condition as above is not attended, after certain few years spalling of concrete takes place on increased corrosion of reinforcement. The chhaja will loose its life. |
- On this development normally chhaja is dismantled, and reinforcement is cut off and chhaja provision is cancelled. |
A. Some times at this location another chhaja of (a) A.C. Sheet, (b) Aluminum, (c) G.I. Sheet, (d) FRP all with wood/ M.S. angel brackets and frame work is provided. Such chhaja has limited life. They are not waterproof at joint and, cause deterioration of concrete and corrosion of reinforcement of adjacent beams/lintels of building. |
B. In this location it is possible to provide a ferrocement chhajas much superior to A.C. sheet, Aluminium, G.I. sheet and FRP. |
(i) Ferrocement chhajas is stronger than RCC and much stronger than Aluminum, G.I., FRP
(ii) The thickness of ferrocement chhajas is 25-30mm.
(iii) It is attached to the building by our anchoring system.
(iv) The chhajas is totally waterproof and junction with building taken special cares to make waterproof.
(v) No repeat waterproofing treatment is required.
(vi) There is considerable dead load reduction.
(vii) Ferrocement chhajas shall last several decades. |
- For some building where RCC balconies collapse due to corrosion and deterioration of concrete, ferrocement balcony is the best solution. Simultaneously there will be dead load reduction and no disturbance and dismantling to inside of room. |
- It is best to provide ferrocement chhaja, lintels, balcony right at the time of building construction. Ferrocement cantilever balcony being less in weight by about 70%, damaging effect by earthquake is the least. |
|
FERROCEMENT – Repair & Rehabilitation |
We carry out inspection study and suggest our own rehabilitation methods and systems, which are far superior to the conventional, as generally described below. |
Ferrocement protective anti-corrosive crack resistant membrane treatment is far superior to guniting because we use wire mesh layers with small dia wires, say 22 g at spacing of about 12 mm center to center and high quality vibrated cement matrix with reactive chemical coatings and finally finished smooth with the surface with the same finish as plaster. |
Another advantage of ferrocement is that this treatment can be carried out in patches such as junction of beams, columns, slabs, bottom of beams, middle portions of beams soffit of slabs, etc., In the case of guniting this is not possible from the practical point of view and perhaps if attempted, the cost will be prohibitive. The finished surface of guniting is rough and particularly in the areas within the building premises another coat of plaster has to be applied, whereas this is not the case in ferrocement. In such case the cost of the work shall come down. |
In the case of epoxy and chemical rehabilitation treatment the surface are required to be highly dust-proof which is generally not possible in repairs and rehabilitation works. Therefore, adhesion may not be as strong as required. |
Secondly epoxy and chemical treated system cannot take large compression, shear and structural stresses. It is found after certain period the members treated with such methods do develop cracks. The epoxy treatment loses strength in case of fire at very low temperature, i.e. about 50 degrees C. |
Therefore, in the long run the structure will start again deteriorating. These types of treatments are non-family material treatment and therefore at some stage or other are likely to be detached. Whereas ferrocement is the same family material as the RCC on which the rehabilitation is required to be carried out and ferrocement is far better in comparison as
described further. |
|
Ferrocement weather shed Vis-à-vis Aluminium/G.I. /A.C. sheet/FRP Weather shed |
Sr.
No. |
Ferrocement Weather Shed of Balcony |
Aluminium/G.I./A.C. sheet/FRP weather shed of balcony |
1 |
Junction of Ferrocement weather shed with beams/ Lintels/pardi is perfectly waterproof. |
The Junction of Aluminium/G.I./A.C. sheet/FRP weather shed is finished with cement mortar vata. This will crack after 4-5 years and required to be redone. In any case there will be leakages of water inside the flat.In due course concrete of lintels /beams /pardi will spall
and reinforcement will corrode. |
2 |
Ferrocement weather shed is connected to lintel, beams, pardi by anchoring and strape connection At the most cantilever anchor beams are provided in case 1.5 -2mtr cantilevers. |
There is no anchoring system in case of Aluminium/G.I./A.C. sheet/FRP weather shed. The
weather shed is supported on wood/ M.S. frame and brackets.
|
3 |
It is very elegant- looks part of the structure. |
It looks dissimilar- much below standard and shall look ugly in comparison. |
4 |
In this weather shed no maintenance is required. |
Has to be repaired after 5-7 years. |
5 |
Ferrocement weather shed is life time provision. |
Has to be replaced after 10-12 years. |
6 |
Dust collection will be there but acceptable. |
Dust collection on FRP weather shed looks very bad from below. |
7 |
There is no corrosion phenomenon. |
Aluminium/G.I. sheet weather shed and M.S. brackets will corrode although painted. |
8 |
Ferrocement weather shed is stronger than Aluminium/G.I./A.C. sheet/FRP weather shed. |
Aluminium/G.I./A.C. sheet/FRP weather shed is much weaker than ferrocement. |
9 |
Ferrocement weather shed is a guaranteed work |
Aluminium/G.I./A.C. sheet/FRP weather shed is not a guaranteed work. |
|
|
Ferrocement Repairs & Rehabilitation
Chhajja Attachments |
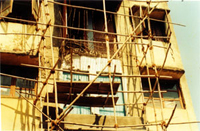 |
Crashed Balcony |
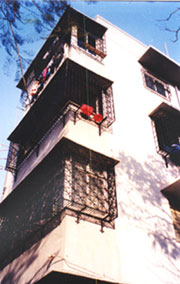 |
Old deteriorated leaking weather shed over balcony replaced with new
ferrocement waterproof weather shed with assured waterproofing at
junction, for Co-Op- Hsg. Society at Vidyavihar.
|
|
|
|
|
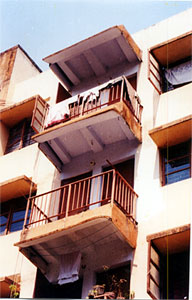 |
Closed view of new Ferrocement Balcony With roof drop pardi And weather Shed |
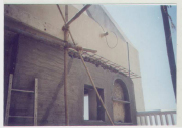 |
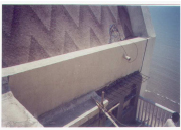 |
Ferrmocement Chajja Attachment to the bungalows. |
|
|
|
|
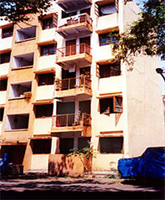 |
Over all view of new set Of ferrocement Balconies From Gr. To 4th floor |
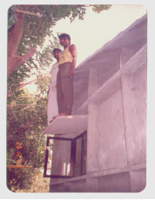 |
Ferrocement Chajja attachment to the window showing load bearing |
|
|
|
|
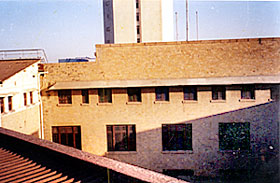 |
Old RCC chhajas 125mm thick replaced with new ferrocement |
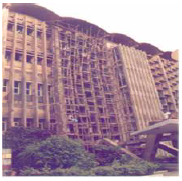 |
Repairs to thin deteriorated RCC fins. Repairs done with method of wrapping of wire mesh layers and high quality vibrated cement matrix. |
|
|
|
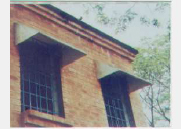 |
Ferrocement Chajja Attachment to the windows of the bungalows. |
|
|
Ferrocement Repairs & Rehabilitation |
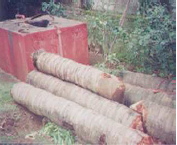 |
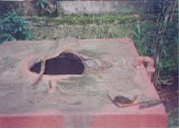 |
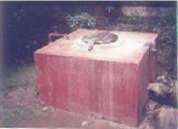 |
A ferrocement water tank could efficiently take onslaught of falling coconut tree with nominal damage in view of high- energy absorbing capacity. The repair cost was a fraction of cost of the tank, which would require total replacement of it was plastic or steel tank. |
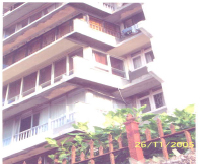 |
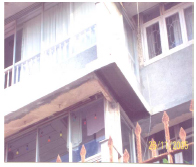 |
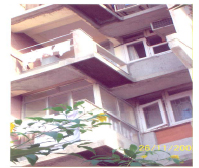 |
Ferrocement Chajjas to cover windows missed originally. |
|
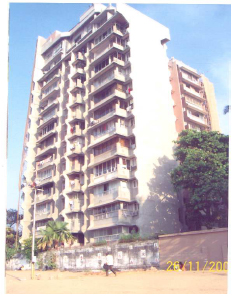 |
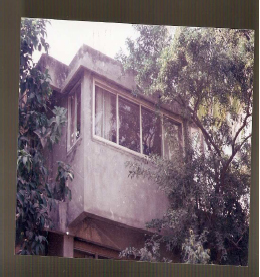 |
Ferrocement Chajjas
to a multi-storey |
Horizontal extension of a room upto 1.5 Mtrs. |
|
Balconies and Chhajja Attachments |
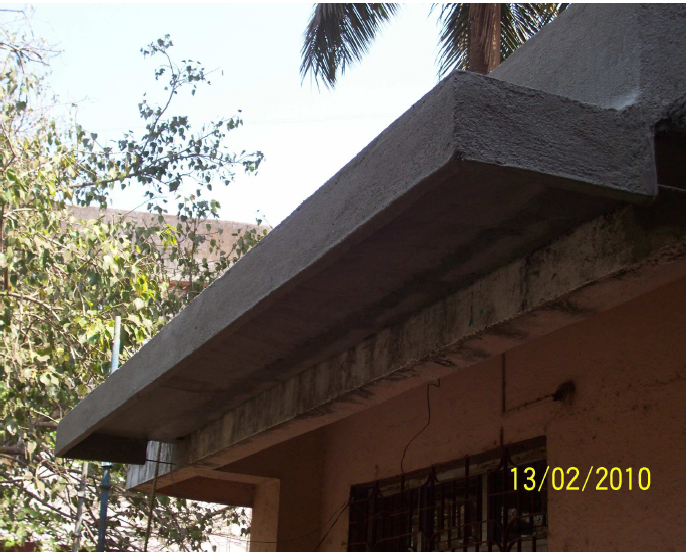 |
|
|